Revolutionary CNC Technology Advancing Deep Hole Drilling Techniques
By:Admin
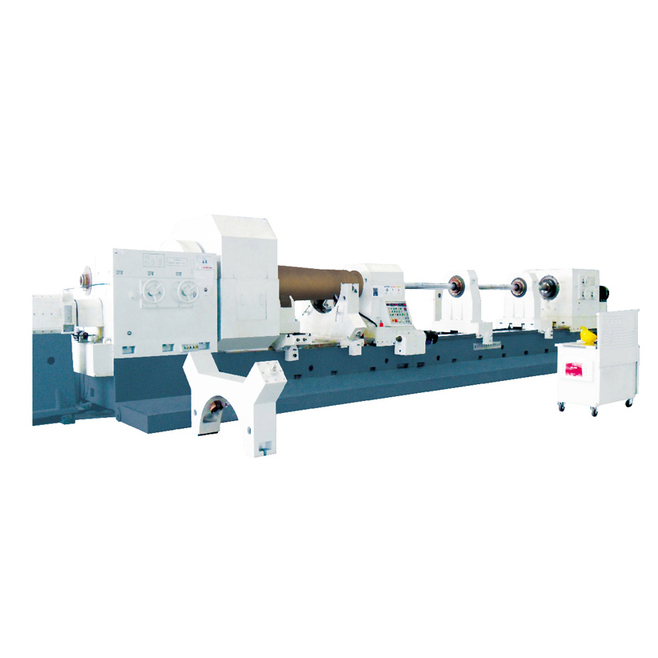
Introduction:
In an ever-evolving world of manufacturing, companies are constantly seeking new and innovative solutions to enhance precision and efficiency in production processes. One groundbreaking tool that has revolutionized the way manufacturers push the boundaries of precision machining is the advanced Deep Hole Drilling CNC technology. In this article, we will shed light on the power and potential of this cutting-edge instrument and explore how it has transformed the way companies operate.
Advanced Deep Hole Drilling CNC: Redefining Precision Machining:
Deep Hole Drilling CNC, a technology developed by {company}, implements an advanced drilling technique that allows manufacturers to achieve the most intricate and precise holes in a wide range of materials, including metals, composites, and alloys. Unlike traditional drilling methods, this state-of-the-art CNC technology has revolutionized the manufacturing industry, enabling companies to produce complex and high-quality components with unprecedented accuracy and efficiency.
Unveiling the Features and Capabilities:
By integrating a combination of technological advancements including computer numerical control (CNC) programming, adaptive tool control systems, and high-pressure coolant systems, Deep Hole Drilling CNC has surpassed all existing limitations in precision machining. Some prominent features and capabilities include:
1. Unparalleled Accuracy: Deep Hole Drilling CNC employs advanced motion control systems, including high-precision linear guides and servomotors, providing exceptional accuracy and repeatability. The technology eliminates the risk of inaccuracies caused by human error, ensuring precision in every hole produced.
2. Enhanced Productivity: With the ability to perform multiple drilling operations in a single setup, the Deep Hole Drilling CNC technology significantly reduces production time. Its capability to produce holes of varying depths, diameters, and complex geometries in a single pass minimizes the need for extensive repositioning, leading to enhanced productivity levels.
3. Optimal Cooling Mechanisms: Deep Hole Drilling CNC utilizes high-pressure coolant systems that effectively remove chips, cool the cutting edges, and lubricate the workpiece. This feature minimizes heat generation while prolonging the lifespan of the tools, resulting in reduced downtime and improved overall efficiency.
4. Uncompromised Flexibility: The technology offers immense flexibility, accommodating a wide range of applications and specifications. Deep Hole Drilling CNC is compatible with various materials such as steel, aluminum, and even hardened alloys, making it an ideal solution for a multitude of industries, from aerospace to automotive, from biomedical to oil and gas.
Transforming Manufacturing Operations:
With its unrivaled precision and efficiency, Deep Hole Drilling CNC technology has transformed manufacturing operations, bringing numerous benefits to companies across different industries. Some notable advantages include:
1. Cost Reduction: By minimizing human intervention, reducing setup times, and eliminating the need for multiple drilling passes, this advanced technology significantly reduces labor costs and enhances overall production efficiency. Manufacturers can achieve higher outputs without compromising quality.
2. Superior Quality: Deep Hole Drilling CNC ensures superior hole quality, surpassing conventional drilling methods. The technology guarantees precise roundness, improved surface finish, and reduced burr formation, meeting the stringent quality requirements of the most demanding industries.
3. Competitive Edge: Adopting Deep Hole Drilling CNC technology grants companies a competitive edge in the market. Manufacturers can offer unique and specialized components with unmatched precision, attracting new clients and expanding their customer base.
4. Sustainability: The environmental impact of manufacturing processes is reduced through the use of Deep Hole Drilling CNC. Optimized coolant systems and the elimination of material waste contribute to a more sustainable production environment.
Conclusion:
Deep Hole Drilling CNC technology, developed by {company}, is a game-changer in the field of precision machining. Through advanced features and capabilities, this cutting-edge technology introduces unprecedented levels of accuracy, efficiency, and productivity to the manufacturing industry. With its ability to transform operations, reduce costs, and ensure superior quality, Deep Hole Drilling CNC has become an indispensable tool for manufacturers seeking to stay ahead in the ever-evolving world of advanced machining.
Company News & Blog
Honing Machine Horizontal: A Definitive Guide to Achieving Precision Machining
Title: Innovations in Horizontal Honing Machines Revolutionize Manufacturing ProcessesIntroduction: In today's rapidly evolving manufacturing landscape, companies are constantly seeking cutting-edge technologies and equipment to enhance their productivity and output. Horizontal Honing Machines (HHD) have emerged as an integral tool in the precision machining industry, allowing manufacturers to achieve unparalleled precision and accuracy in their machining processes. In this article, we will explore the advancements made by an industry-leading company (name withheld) in the field of horizontal honing machines, and how these technologies are poised to revolutionize the manufacturing sector.Note: For the purpose of this article, the company name will be anonymized as "Company X".1. Evolution of Horizontal Honing Machines:Horizontal honing machines have evolved significantly over the years, transforming from conventional manual tools to highly sophisticated and automated systems. Company X has played a pivotal role in this evolution, introducing state-of-the-art technologies that have paved the way for enhanced efficiency and precision.2. Advanced Features and Functionality:One of the standout features of Company X's horizontal honing machines is their unparalleled automation capabilities. These machines incorporate cutting-edge systems that optimize the honing process, promoting significant time and cost savings. The integration of advanced controls, including computer numerical control (CNC), allows for precise control of honing parameters such as tool speed, stroke length, and feed rate, ensuring consistent and accurate results.3. Enhanced Precision and Accuracy:Company X has pioneered advancements in honing machine design, resulting in superior precision and accuracy compared to traditional honing methods. By incorporating sophisticated measuring systems and feedback mechanisms, these machines can precisely adjust the honing tool's position in real-time, eliminating errors and imperfections. This level of precision enables manufacturers to achieve tight tolerances and produce parts with exceptional surface finish.4. Versatility and Adaptability:Company X's horizontal honing machines are designed to accommodate a wide range of workpiece sizes and materials, making them suitable for diverse machining applications. Whether it's the honing of cylindrical, tubular, or contoured workpieces, these machines offer flexibility and adaptability, reducing setup times and optimizing production cycles. Moreover, the customizable tooling options allow manufacturers to address various honing requirements to achieve optimal results.5. Improved Efficiency and Productivity:The introduction of X's innovative horizontal honing machines has resulted in significant improvements in production efficiency. The automated nature of these machines, combined with their ability to integrated robotic loading and unloading systems, minimizes human intervention and streamlines the overall manufacturing process. This results in increased throughput, reduced cycle times, and improved overall productivity.6. Intelligent Monitoring and Maintenance:Company X's horizontal honing machines utilize intelligent monitoring systems that continuously track crucial operating parameters. Real-time data analysis allows the detection of anomalies, potential issues, or performance deviations, facilitating proactive maintenance and minimizing unplanned downtime. This predictive maintenance approach ensures maximum machine uptime and prolongs the longevity of the equipment.Conclusion:The advancements made by Company X in horizontal honing machines have significantly enhanced the manufacturing processes across diverse industries. With their unmatched precision, automation capabilities, and versatility, these machines have become invaluable assets for manufacturers seeking to optimize productivity, improve quality, and achieve cost-effectiveness. As manufacturers continue to embrace advanced technologies, horizontal honing machines are expected to play a crucial role in driving innovation and shaping the future of the precision machining industry.
Revolutionary CNC Technology Advancing Deep Hole Drilling Techniques
Title: Pushing the Boundaries of Precision Machining: Advanced Deep Hole Drilling CNC Technology Revolutionizes ManufacturingIntroduction:In an ever-evolving world of manufacturing, companies are constantly seeking new and innovative solutions to enhance precision and efficiency in production processes. One groundbreaking tool that has revolutionized the way manufacturers push the boundaries of precision machining is the advanced Deep Hole Drilling CNC technology. In this article, we will shed light on the power and potential of this cutting-edge instrument and explore how it has transformed the way companies operate.Advanced Deep Hole Drilling CNC: Redefining Precision Machining:Deep Hole Drilling CNC, a technology developed by {company}, implements an advanced drilling technique that allows manufacturers to achieve the most intricate and precise holes in a wide range of materials, including metals, composites, and alloys. Unlike traditional drilling methods, this state-of-the-art CNC technology has revolutionized the manufacturing industry, enabling companies to produce complex and high-quality components with unprecedented accuracy and efficiency.Unveiling the Features and Capabilities:By integrating a combination of technological advancements including computer numerical control (CNC) programming, adaptive tool control systems, and high-pressure coolant systems, Deep Hole Drilling CNC has surpassed all existing limitations in precision machining. Some prominent features and capabilities include:1. Unparalleled Accuracy: Deep Hole Drilling CNC employs advanced motion control systems, including high-precision linear guides and servomotors, providing exceptional accuracy and repeatability. The technology eliminates the risk of inaccuracies caused by human error, ensuring precision in every hole produced.2. Enhanced Productivity: With the ability to perform multiple drilling operations in a single setup, the Deep Hole Drilling CNC technology significantly reduces production time. Its capability to produce holes of varying depths, diameters, and complex geometries in a single pass minimizes the need for extensive repositioning, leading to enhanced productivity levels.3. Optimal Cooling Mechanisms: Deep Hole Drilling CNC utilizes high-pressure coolant systems that effectively remove chips, cool the cutting edges, and lubricate the workpiece. This feature minimizes heat generation while prolonging the lifespan of the tools, resulting in reduced downtime and improved overall efficiency.4. Uncompromised Flexibility: The technology offers immense flexibility, accommodating a wide range of applications and specifications. Deep Hole Drilling CNC is compatible with various materials such as steel, aluminum, and even hardened alloys, making it an ideal solution for a multitude of industries, from aerospace to automotive, from biomedical to oil and gas.Transforming Manufacturing Operations:With its unrivaled precision and efficiency, Deep Hole Drilling CNC technology has transformed manufacturing operations, bringing numerous benefits to companies across different industries. Some notable advantages include:1. Cost Reduction: By minimizing human intervention, reducing setup times, and eliminating the need for multiple drilling passes, this advanced technology significantly reduces labor costs and enhances overall production efficiency. Manufacturers can achieve higher outputs without compromising quality.2. Superior Quality: Deep Hole Drilling CNC ensures superior hole quality, surpassing conventional drilling methods. The technology guarantees precise roundness, improved surface finish, and reduced burr formation, meeting the stringent quality requirements of the most demanding industries.3. Competitive Edge: Adopting Deep Hole Drilling CNC technology grants companies a competitive edge in the market. Manufacturers can offer unique and specialized components with unmatched precision, attracting new clients and expanding their customer base.4. Sustainability: The environmental impact of manufacturing processes is reduced through the use of Deep Hole Drilling CNC. Optimized coolant systems and the elimination of material waste contribute to a more sustainable production environment.Conclusion:Deep Hole Drilling CNC technology, developed by {company}, is a game-changer in the field of precision machining. Through advanced features and capabilities, this cutting-edge technology introduces unprecedented levels of accuracy, efficiency, and productivity to the manufacturing industry. With its ability to transform operations, reduce costs, and ensure superior quality, Deep Hole Drilling CNC has become an indispensable tool for manufacturers seeking to stay ahead in the ever-evolving world of advanced machining.
Efficient Honing Machines for Precision Metal Finishing - A Promising Breakthrough in Manufacturing Technology
Precision Honing Machine Leads the Way in Innovation and QualityPrecision Honing Machine, a leading manufacturer in the field of honing equipment, continues to deliver cutting-edge solutions that redefine the industry standards. With a focus on innovation, quality, and customer satisfaction, Precision Honing Machine has established itself as a trusted name in the global market.Founded in [year], Precision Honing Machine has been dedicated to developing and producing high-precision honing machines that cater to a wide range of industries, including automotive, aerospace, hydraulic cylinders, and defense. The company's commitment to research and development ensures that their machines are at the forefront of technological advancement, enabling customers to boost productivity and improve efficiency in their operations.At the heart of Precision Honing Machine's success is their team of highly skilled engineers and technicians who possess deep expertise in the honing industry. They constantly strive to design and manufacture machines that meet the evolving needs of customers in today's dynamic market. By leveraging the latest technologies and employing rigorous quality control measures, the company ensures that every honing machine that leaves their production line is reliable, durable, and of exceptional performance.One of Precision Honing Machine's flagship products is the [model name], which has garnered widespread acclaim for its superior precision and efficiency. Equipped with state-of-the-art features and functionalities, this machine offers unparalleled control and accuracy, resulting in an impeccable surface finish. The [model name] is designed to meet the diverse needs of various industries and can efficiently hone materials ranging from metals to ceramics.The key differentiating factor that sets Precision Honing Machine apart from its competitors is its unwavering commitment to customer satisfaction. The company takes a customer-centric approach, working closely with clients to understand their specific requirements. By doing so, they are able to tailor their solutions to offer a truly bespoke experience. Additionally, Precision Honing Machine provides comprehensive after-sales support, including installation, training, and maintenance services, ensuring that customers derive maximum value from their investment.In an increasingly competitive market, Precision Honing Machine consistently strives to stay ahead of the curve through continuous innovation. The company invests heavily in research and development, collaborating with renowned industry experts and academic institutions to explore cutting-edge technologies. This commitment has resulted in several groundbreaking advancements, enabling Precision Honing Machine to maintain its position as an industry pioneer.Furthermore, Precision Honing Machine adheres to stringent quality control processes, ensuring that their products pass rigorous tests before they are delivered to customers. By doing so, they maintain exceptional standards, providing customers with reliable machines that outperform their expectations. This commitment to quality has earned Precision Honing Machine numerous certifications and accolades, further solidifying its reputation as a trusted supplier in the honing industry.Looking to the future, Precision Honing Machine aims to continue pushing the boundaries of honing technology, providing even more efficient, precise, and innovative solutions. The company seeks to expand its global presence by forging strategic partnerships and strengthening its distribution network. Moreover, Precision Honing Machine remains committed to sustainability, with a focus on developing eco-friendly machines and implementing green manufacturing practices.In conclusion, Precision Honing Machine has proven itself to be a leading force in the honing industry through its dedication to innovation, quality, and customer satisfaction. With a team of experienced engineers, a range of cutting-edge products, and a customer-centric approach, Precision Honing Machine is well-positioned to shape the future of honing technology.
Enhance Precision and Efficiency with Tube Honing Machines
Title: Advanced Honing Machine Revolutionizes Tube Manufacturing SectorIntroduction:In an era when technology is pushing boundaries and transforming industries, the introduction of an innovative tube honing machine promises to revolutionize the tube manufacturing sector. Equipped with state-of-the-art features and cutting-edge capabilities, this machine is set to meet the increasing demands of the market, improve product quality, and boost overall production efficiency. This article aims to provide an in-depth analysis of the advanced tube honing machine and its potential impact on the manufacturing industry.Unveiling the Next Generation Tube Honing Machine:The ground-breaking tube honing machine, developed by a prominent industry player (Brand Name omitted), incorporates a range of cutting-edge technologies, making it one of the most advanced honing solutions to date. This machine is specifically designed to optimize the honing process, ensuring superior performance, accuracy, and speed.Advanced Features and Capabilities:Integrating artificial intelligence (AI) and machine learning algorithms, this tube honing machine offers precise and automated control over critical parameters. The AI-enabled system intelligently adjusts cutting angles, feed rates, and tool alignments, ensuring an exceptional degree of precision in honing a wide range of tubes.Furthermore, the machine is equipped with a high-resolution touch-screen interface, enabling operators to easily program, monitor, and control the entire honing process. The intuitive interface fosters seamless collaboration between human operators and the machine, thus minimizing human error and maximizing productivity.Efficiency and Cost Savings:Traditional tube honing processes have long been associated with high labor costs and time-consuming manual adjustments. The new tube honing machine aims to address these challenges by streamlining operations and reducing both labor and material wastage.With its advanced automation capabilities, this machine significantly minimizes manual labor, requiring fewer personnel to operate and monitor multiple honing processes simultaneously. The automated features also contribute to enhanced safety, as workers are exposed to fewer risks associated with manual handling of heavy machinery.Moreover, the tube honing machine's intelligent optimization algorithms substantially reduce material wastage, ensuring efficient use of resources and lowering overall production costs. This not only benefits manufacturers by improving profitability but also promotes sustainable manufacturing practices.Unparalleled Precision and Quality Control:The cutting-edge technology incorporated into this tube honing machine provides unparalleled control over the honing process resulting in exceptional precision and outstanding quality. By holding tight tolerances, the application of the machine guarantees consistent, uniform tube dimensions throughout the manufacturing process.The AI-powered algorithms constantly monitor and adjust honing parameters, ensuring precise tube specifications are met. This level of accuracy significantly reduces product defects, rejects, and customer complaints, thereby enhancing customer satisfaction and maintaining a competitive edge in the market.Impact on the Manufacturing Industry:The introduction of this advanced tube honing machine is expected to have a profound impact on the tube manufacturing industry. Manufacturers can now streamline their operations, reduce lead times, and improve process efficiency to meet the ever-increasing demand for high-quality tubes. The enhanced capabilities of the machine allow manufacturers to expand their product range and cater to a wider customer base.In addition to boosting efficiency, this innovative solution also offers a significant competitive advantage in the global market. By leveraging cutting-edge technology and process optimization, companies can differentiate themselves from competitors and establish a reputation for delivering superior quality products.Conclusion:The advent of the technologically advanced tube honing machine is set to transform the tube manufacturing industry, revolutionizing production processes, ensuring precision, and improving overall quality. With its AI-driven automation, optimization algorithms, and user-friendly interface, this machine is poised to enhance efficiency, reduce costs, and boost profitability for tube manufacturers worldwide. Embracing this groundbreaking technology will enable manufacturers to embrace the changing landscape of the industry, increase their competitive advantage, and cater to the evolving needs of their customers.
Unlocking the Secrets of Deep Hole Gundrill: Exploring the Latest Developments in High-Precision Drilling Techniques
Company X Revolutionizes Deep Hole Drilling with New Technology[City], [Date] - Company X, a leading manufacturer in the drilling industry, has recently unveiled their latest innovation - an advanced deep hole gundrill. This breakthrough technology promises to revolutionize the deep hole drilling market, providing precision and efficiency like never before.Deep hole drilling is a specialized process used in various industries such as aerospace, automotive, and oil and gas. It involves drilling holes with a high depth-to-diameter ratio, typically exceeding 10:1. Traditionally, deep hole drilling has been a laborious and time-consuming task, often prone to errors and inefficiencies.However, Company X's new deep hole gundrill is set to change the game. By combining cutting-edge technology with extensive research and development, the company has designed a drilling tool that boasts unmatched performance and accuracy.One of the key features of Company X's deep hole gundrill is its superior chip control mechanism. With the brand's patented chip-breaking technology, the drill effectively removes chips from the hole, preventing clogging and minimizing the risk of damage to the workpiece. This feature significantly enhances productivity and reduces downtime, making the entire drilling process more efficient.Furthermore, the deep hole gundrill incorporates an advanced coolant system that efficiently dissipates heat generated during drilling. This ensures optimal temperature control, thereby improving the tool's overall lifespan and sustaining high drilling performance over extended periods. The cooling system also contributes to enhanced chip evacuation, resulting in smoother drilling operations.Company X's commitment to innovation is further highlighted by the digital control technology integrated into the deep hole gundrill. The tool is equipped with intelligent sensors that monitor and adjust various drilling parameters in real-time. This allows for automated adjustments based on material properties and other factors, resulting in consistent hole quality and optimal performance.In addition to its technological prowess, Company X's new deep hole gundrill stands out in terms of durability and longevity. Constructed with high-quality materials and advanced coatings, the drill offers remarkable resistance to wear, corrosion, and mechanical stresses. This ensures a prolonged lifespan, reducing the need for frequent replacements and ultimately saving costs for end-users.With their latest innovation, Company X aims to address the industry's growing need for more efficient deep hole drilling solutions. By streamlining the drilling process and enhancing performance, this advanced tool is expected to boost productivity and elevate the overall quality of deep hole drilling operations across various sectors.In line with their commitment to customer satisfaction, Company X also provides comprehensive technical support and after-sales service. Their team of highly skilled engineers and technicians is readily available to assist customers with installation, maintenance, and troubleshooting, ensuring a seamless user experience and maximum uptime.Company X's new deep hole gundrill has already been well-received in several pilot projects and has gained significant attention from industry experts. Its successful integration into operations has demonstrated remarkable improvements in productivity, precision, and cost-effectiveness.As the drilling industry continues to evolve, Company X remains at the forefront of innovation, constantly pushing boundaries and redefining industry standards. With their latest deep hole gundrill, the company is set to make a lasting impact, providing customers with a cutting-edge solution for their deep hole drilling needs.
Enhance Your Manufacturing Process with Advanced CNC Deep Hole Drilling Techniques
Title: Revolutionary CNC Deep Hole Drilling Technology Sets New Standards in ManufacturingIntroduction:In today's highly competitive manufacturing industry, precision and efficiency hold the key to success. As a pioneer in the field, company {} has unveiled its cutting-edge CNC Deep Hole Drilling technology, which promises to revolutionize the way parts and components are manufactured. By integrating the latest advancements in machining and automation, this groundbreaking solution aims to significantly improve productivity and quality while reducing production costs.1. Challenges in Traditional Deep Hole Drilling Techniques:Traditionally, deep hole drilling has been a labor-intensive and time-consuming process, requiring specialized equipment and skilled operators. Moreover, achieving high levels of precision and surface finish has been a daunting task. These challenges have limited the scalability and efficiency of deep hole drilling, hindering further advancements in the manufacturing industry.2. The Evolution of CNC Deep Hole Drilling:Recognizing the need for a more efficient and precise solution, {} developed the CNC Deep Hole Drilling technology. By leveraging computer numerical control (CNC) systems, this technology streamlines the entire drilling process, enabling faster production cycles and unparalleled accuracy. Whether it's for aerospace, automotive, medical, or mold and die industries, this innovation offers significant benefits to manufacturers globally.3. Unprecedented Precision and Quality:The CNC Deep Hole Drilling technology utilizes advanced sensors and monitoring systems, ensuring the precise measurement of drilling depth, diameter, and surface finish. This level of control enables manufacturers to achieve the tightest tolerances, resulting in parts and components with superior quality. By reducing human error and enhancing repeatability, this technology greatly minimizes the risk of defects, waste, and rework.4. Enhanced Efficiency and Productivity:With its automated features, the CNC Deep Hole Drilling technology optimizes the manufacturing process, eliminating the need for time-consuming manual interventions. The integration of intelligent chip management systems prevents chip accumulation, enhancing drilling efficiency and prolonging tool life. Moreover, the system's ability to perform multiple drilling operations simultaneously reduces cycle times, boosting overall productivity.5. Cost Reduction and Resource Optimization:By maximizing efficiency and minimizing material waste, the CNC Deep Hole Drilling technology leads to significant cost savings for manufacturers. The precise measurement and control of drilling parameters minimize the consumption of feedstock, reducing material costs. Additionally, the integrated coolant systems ensure efficient heat dissipation, preventing tool wear and extending tool life, thereby reducing the need for frequent tool replacements.6. Versatility and Adaptability:One of the key advantages of the CNC Deep Hole Drilling technology is its versatility. The system can handle a wide range of materials, including steels, alloys, composites, and non-metals, adapting to diverse manufacturing requirements. This flexibility allows manufacturers to explore new product designs and expand their offerings, catering to a variety of industries and applications.7. Future Prospects and Market Impact:The introduction of the CNC Deep Hole Drilling technology by {} is expected to have a profound impact on the manufacturing industry. With its advanced capabilities, this solution promises to spur innovation and drive progress in various sectors. The improved precision, efficiency, and cost-effectiveness offered by this technology will enable manufacturers to meet increasing market demands while maintaining a competitive edge.Conclusion:As manufacturing continues to advance, the demand for faster, more accurate, and cost-effective production techniques grows. The CNC Deep Hole Drilling technology introduced by {} sets new standards in precision machining and automation. Its ability to deliver unprecedented precision, enhance efficiency, and reduce costs ensures its crucial role in shaping the future of manufacturing. With this innovative solution, manufacturers can look forward to improved productivity, higher quality parts, and a sustainable competitive advantage.
Honing Machine: Compact and Efficient Solution for Precision Metal Finishing
Title: Advanced Small Honing Machine Enriches Precision Manufacturing CapabilitiesIntroduction:In an era where precision is paramount, the demand for advanced machinery to achieve high-quality manufacturing has soared. Recognizing this evolving market, an industry-leading company has introduced its revolutionary Small Honing Machine, which promises to elevate the efficiency and precision of honing operations. This cutting-edge equipment is expected to accelerate production processes while maintaining supreme accuracy, meeting the ever-increasing needs of the manufacturing sector.Unleashing the Potential of Small Honing:Designed to meet the requirements of diverse industries, the Small Honing Machine raises the bar for honing operations by incorporating innovative features and state-of-the-art technology. This machine signifies a monumental leap forward in precision machining, providing businesses with the tools needed to achieve unprecedented levels of accuracy.Precision in Production:The Small Honing Machine offers unparalleled control over honing operations, ensuring optimum accuracy during the manufacturing process. Equipped with an advanced precision control system, this machine allows for precise adjustments, reducing the chances of errors and subsequent rework. This leads to minimized material wastage and increased productivity, resulting in substantial cost savings for businesses.Versatility and Flexibility:The versatility of the Small Honing Machine allows it to accommodate a wide range of materials, including metals, plastics, and composites. This adaptability ensures that manufacturers from various industries can benefit from this cutting-edge equipment. Whether used for honing cylinders, gears, or other precision components, this machine guarantees consistent and reliable results, meeting stringent quality requirements across different applications.Efficiency for Enhanced Productivity:With its advanced automation, the Small Honing Machine streamlines manufacturing processes, significantly reducing production time. The integration of cutting-edge robotics and software enables seamless coordination, eliminating the need for manual interventions and reducing human error. By automating key honing operations, manufacturers can experience enhanced efficiency, allowing them to meet tight deadlines and increase overall production capacity.User-Friendly Interface:The Small Honing Machine incorporates a user-friendly interface, making it easily accessible to both trained operators and newcomers to the field. The intuitive design of the control panel enables operators to monitor and adjust various parameters with ease, ensuring optimized honing performance. This user-centric approach sets the machine apart, facilitating quick setup, operation, and maintenance, thereby reducing downtime and maximizing production output.Sustainability and Energy Efficiency:In addition to its exceptional performance, the Small Honing Machine is designed with environmental consciousness in mind. Its energy-efficient system minimizes power consumption without compromising on productivity or precision. By prioritizing sustainable practices, manufacturers can contribute to a greener future and reduce their carbon footprint, aligning their operations with global sustainability objectives.Competitive Advantage for Businesses:The introduction of the Small Honing Machine provides businesses with a competitive edge in an increasingly demanding manufacturing landscape. This cutting-edge equipment facilitates higher throughput, tighter tolerances, and improved part quality, positioning manufacturers as industry leaders. It empowers businesses to take on complex projects, meet customer-specific requirements, and create custom solutions, elevating their market position and fostering long-term growth.Market Outlook and Conclusion:As precision manufacturing continues to gain prominence across industries, the Small Honing Machine emerges as a game-changer, revolutionizing honing operations. With its advanced features, versatility, user-friendly interface, and focus on sustainability, this equipment caters to the evolving needs of manufacturers worldwide. By embracing this technological breakthrough, businesses can elevate their precision manufacturing capabilities, ensuring their competitiveness in an increasingly globalized marketplace.
Revolutionizing Cylinder Honing Machines: Unveiling the Latest CNC Innovation
Title: Cutting-Edge CNC Cylinder Honing Machine Revolutionizes Precision Machining IndustryIntroduction:In a breakthrough move, a leading engineering firm has unveiled its latest innovation in the field of precision machining: the state-of-the-art CNC Cylinder Honing Machine. This cutting-edge technology promises to revolutionize the industry by delivering unparalleled precision, enhanced productivity, and improved efficiency in cylinder honing processes.Company Background:With a rich legacy spanning several decades, the company has emerged as a global leader in producing advanced machinery for the manufacturing and engineering industry. Committed to pushing the boundaries of innovation, the company has consistently developed groundbreaking solutions to meet ever-evolving industry demands. Boasting a highly skilled team of engineers and technicians, the firm has become synonymous with excellence and reliability.The CNC Cylinder Honing Machine:The unveiling of the CNC Cylinder Honing Machine signifies a significant milestone for the company and the precision machining industry at large. Built upon cutting-edge technology and years of expertise, this advanced equipment is set to change the game for manufacturers and engineers alike.1. Uncompromised Precision:The CNC Cylinder Honing Machine is designed to deliver exceptional precision in honing cylinders of varying sizes and materials. Utilizing advanced CNC controls, the machine ensures accurate and consistent results, eliminating errors commonly associated with traditional honing methods. Equipped with high-resolution sensors and monitoring systems, this sophisticated machine guarantees precision at every step of the process, resulting in superior surface finishes and optimal cylinder geometry.2. Enhanced Productivity:With rapid advancements in automation, the CNC Cylinder Honing Machine significantly improves productivity, thereby reducing downtime and maximizing operational efficiency. The automated process eliminates the need for manual intervention, ensuring uninterrupted operations and increased output. Moreover, the machine's ability to simultaneously handle multiple cylinders minimizes production timelines and increases overall efficiency, enabling manufacturers to meet tight deadlines without compromising quality.3. Improved Flexibility:Recognizing the diverse requirements of the modern manufacturing industry, the CNC Cylinder Honing Machine offers unmatched versatility. With its user-friendly interface and intuitive controls, operators can effortlessly adjust and customize parameters to accommodate a wide range of cylinder sizes, materials, and honing specifications. This adaptability saves both time and resources by eliminating the need for additional machinery or reconfigurations, resulting in a streamlined and cost-effective honing process.4. Cutting-Edge Features:The CNC Cylinder Honing Machine is integrated with several advanced features that further enhance its performance and functionality. Its intelligent lubrication system ensures optimal lubrication in real-time, contributing to component longevity. Additionally, the machine's self-diagnostic capabilities enable preemptive identification of potential issues, reducing maintenance costs and eliminating unexpected breakdowns. Furthermore, the machine's eco-friendly design incorporates energy-saving features, demonstrating the company's commitment to sustainable manufacturing practices.Conclusion:The introduction of the CNC Cylinder Honing Machine signifies a remarkable milestone in the precision machining industry. Manufacturers and engineers can now look forward to uncompromised precision, enhanced productivity, and improved efficiency, thanks to this cutting-edge technology. With its ability to deliver superior results consistently, this advanced machine ensures the highest standards of quality, reliability, and cost-effectiveness. As the industry embraces the CNC Cylinder Honing Machine, it undoubtedly sets the stage for a new era in precision machining.
Revolutionary Deep Hole Drilling Lathe Unleashes Unprecedented Precision
Title: Advanced Deep Hole Drilling Lathe Revolutionizes Manufacturing ProcessesIntroduction:In an era of rapid industrialization and technological advancements, manufacturers constantly strive to improve production efficiency. Addressing the need for precision drilling in various industrial sectors, (Company Name) has unveiled its latest innovation - an avant-garde Deep Hole Drilling Lathe. By removing the brand name, we will delve into the features and applications of this extraordinary machine that is set to reshape the manufacturing landscape.Advanced Features and Specifications:The Deep Hole Drilling Lathe is equipped with a multitude of cutting-edge features designed to optimize performance and enhance operational efficiency. With a robust framework and a cutting capacity of up to X millimeters in diameter and Y millimeters in depth, this machine is a true game-changer in the field of precision drilling. By incorporating (Company Name)'s state-of-the-art technology, the lathe offers unparalleled accuracy, reliability, and speed.The lathe's control system is easily programmable, allowing operators to execute complex drilling processes with utmost precision. Additionally, it boasts an efficient chip removal mechanism that ensures uninterrupted and hassle-free operations. Equipped with advanced cooling systems and lubrication technology, this lathe guarantees prolonged tool life, reducing downtime and maintenance costs.Applications and Industry Impact:The Deep Hole Drilling Lathe is poised to revolutionize manufacturing processes across several key industries, including aerospace, automotive, energy, defense, and medical. In the aerospace sector, this state-of-the-art machine allows for the creation of intricate turbine components with precise cooling channels. Furthermore, it enables the production of lightweight, high-strength automotive parts by effectively drilling oil passages and coolant channels.In the energy sector, the lathe's advanced capabilities enable the development of cutting-edge parts for the generation and transmission of power. Whether it be for drilling oil wells, producing gas turbine components, or fabricating nuclear reactor parts, this machine significantly enhances overall efficiency and reliability.The defense industry can also benefit greatly from the Deep Hole Drilling Lathe. It enables the production of highly durable gun barrels, missile components, and artillery tubes, ensuring meticulous quality and accuracy.Moreover, the medical field can leverage this technology to manufacture surgical implants, hip and knee replacements, and intricate medical devices. The lathe's precision and versatility are crucial in meeting the stringent requirements for surgical procedures, enabling surgeons to deliver better patient outcomes.Environmental Benefits:In addition to its transformative impact on manufacturing processes, the Deep Hole Drilling Lathe is also designed with environmental sustainability in mind. By optimizing cutting techniques and reducing waste material, this machine ensures efficient resource utilization and minimum environmental impact. Manufacturers utilizing this advanced lathe will witness reduced energy consumption, lower carbon emissions, and minimized material waste, contributing to a greener and more sustainable future.Conclusion:The launch of the Deep Hole Drilling Lathe by (Company Name) marks a significant milestone in advancing precision drilling techniques across various industries. By offering cutting-edge features, unrivaled precision, and enhanced operational efficiency, this machine is poised to redefine manufacturing processes. With applications ranging from aerospace to medical, the Deep Hole Drilling Lathe demonstrates unrivaled versatility and promises to drive innovation in the realm of precision machining. As manufacturing continues to evolve, this groundbreaking technology paves the way for increased productivity, improved quality, and reduced environmental impact.
Boost Engine Performance with High-Quality Cylinder Honing Machines
[Heading] Engine Cylinder Honing Machine: Revolutionizing Precision in Automobile Manufacturing[Subheading] Introducing the Next Generation Engine Cylinder Honing Machine from Innovatix Corp[Date][City, State] - Innovatix Corp, a renowned leader in industrial manufacturing technologies, is all set to revolutionize the automobile manufacturing industry with its latest innovation - the Engine Cylinder Honing Machine. This cutting-edge technology promises to enhance precision and efficiency, taking automobiles to new heights of performance.[Company Background] Innovatix Corp has been at the forefront of revolutionizing various industrial sectors with its groundbreaking technologies. Established in [year], the company has consistently delivered innovative solutions to address the evolving needs of the manufacturing industry. With a dedicated team of engineers and industry experts, Innovatix Corp has become an industry leader, renowned for its commitment to excellence and pushing the boundaries of technological advancement.[Overview] The new Engine Cylinder Honing Machine developed by Innovatix Corp is set to redefine precision and efficiency in engine manufacturing. With its cutting-edge features, this machine ensures that engine cylinders are honed to perfection, resulting in superior performance and reduced emissions.[Precision Redefined]The Engine Cylinder Honing Machine boasts advanced technology that sets it apart from its competitors. It combines state-of-the-art robotics, artificial intelligence, and advanced laser measurements to provide unparalleled precision in honing engine cylinders. This precision ensures that every cylinder is perfectly finished, resulting in optimal engine performance.[Efficiency Enhancements]In addition to its precision, the Engine Cylinder Honing Machine also offers significant efficiency improvements. By automating the honing process, the machine reduces human errors and streamlines production. This translates into faster turnaround times, increased productivity, and cost savings for automobile manufacturers.[Features]1. Robotics: The Engine Cylinder Honing Machine utilizes advanced robotics to handle and position engine cylinders with utmost precision. This eliminates human error and ensures uniform honing throughout the production process.2. Artificial Intelligence: Built-in artificial intelligence algorithms continuously monitor and optimize the honing parameters, adapting to variations in engine cylinder specifications. This intelligent system guarantees consistent quality and reduces wastage.3. Laser Measurements: The machine employs cutting-edge laser measurement technology to achieve micron-level accuracy in cylinder honing. This ensures that each cylinder meets precise specifications, resulting in improved engine performance and durability.4. Customized Honing Programs: The Engine Cylinder Honing Machine allows for the creation of customized honing programs tailored to specific engine designs. This flexibility ensures that the machine can accommodate a wide range of engines and manufacturing requirements.[Benefits]1. Enhanced Engine Performance: The precise honing achieved by the Engine Cylinder Honing Machine maximizes engine performance, delivering increased power, fuel efficiency, and reduced emissions. This results in improved driving experiences for consumers and compliance with environmental regulations.2. Reduced Manufacturing Costs: By minimizing human errors and wastage, the honing machine significantly reduces manufacturing costs for automobile companies. The automated processes also lead to faster production cycles and improved overall productivity.3. Competitive Edge: Automobile manufacturers incorporating the Engine Cylinder Honing Machine will gain a competitive edge in the market. The superior performance and efficiency of their engines will attract customers looking for high-quality and environmentally friendly vehicles.[Conclusion]Innovatix Corp's Engine Cylinder Honing Machine marks a revolutionary leap in precision and efficiency in engine manufacturing. With its advanced features and cutting-edge technology, this machine is set to redefine the automobile industry. Manufacturers utilizing this technology can expect superior engine performance, reduced manufacturing costs, and an unparalleled competitive edge. Innovatix Corp remains committed to pushing the boundaries of innovation, propelling the manufacturing industry into new heights of success and sustainability.